December 14, 2024
Injection mold new technology and new technology
Injection molding applies pressure to molten fluid plastic using metal materials to form a cavity in the shape of the part. The machine injects the molten plastic into the cavity and maintains the pressure for a certain period. After cooling the plastic melt, the machine removes the finished part.
Injection molding generally relies on an injection molding machine and the corresponding mold. The granular plastic in the injection molding machine’s barrel heats up to a molten, flowable state. The plunger or screw in the injection molding machine applies pressure, compressing the plastic melt into the nozzle at the head of the barrel. The machine quickly injects the melt into the cavity of the closed mold and maintains the pressure for some time. After cooling and shaping, the mold opens, and we take out the finished product.
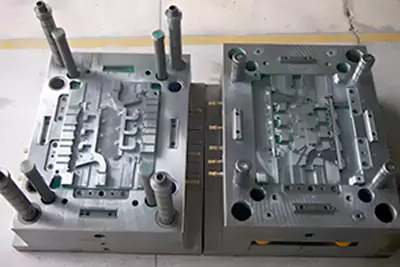
This is an intermittent operation process. Most injection molding machines are horizontal, and manufacturers make injection molds from steel, aluminum, or other metals.
Injection molding manufactures various parts, most of which are plastic products. These range from plastic gear in toys to different white goods. The injection molding process includes five steps:
(1)The mold forms a cavity.
(2)The plunger or screw feeds the plastic melt into the cavity.
(3) The operator maintains the pressure inside the cavity, allowing the plastic melt to set.
(4) The operator regulates the mold temperature.
(5) The operator opens the mold cavity and removes the product.
In recent years, traditional mold production and processing technology has failed to meet market demands. Industrial development requires new technologies to enhance labor productivity and technical content.
Foam Injection Molding Technology
Foam injection molding technology is divided into physical and chemical foam types. In physical foaming, the process injects molten plastic particles into nitrogen or carbon dioxide gas at a supercritical point. They mix and diffuse under pressure into the cavity, forming microcellular foamed parts. In chemical foaming, manufacturers add a blowing agent to the molten plastic granules. This blowing agent foams inside the material, filling the mold cavity and forming the part with internal pores and a tough skinlike surface.
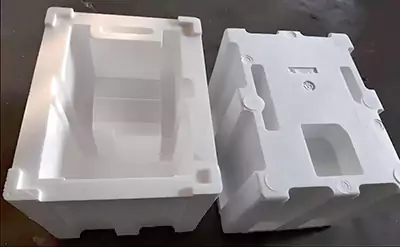
Physical foam molding typically forms bubbles smaller than 50 μm and distributes them uniformly. The density is generally greater than 110/cm³. Chemical foaming is used for thick-walled parts greater than 5 mm, and it produces bubbles larger than 100 μm that distribute unevenly.
Advantages of Foam Injection Molding:
Reduces weight, with plastic products maintaining mechanical properties. It can reduce the weight by 5% to 30%.
Eliminates surface defects like shrinkage marks for parts with a wall thickness ratio of less than or equal to 1.
Requires less injection molding pressure, reducing the clamping force and shortening the molding cycle.
Reduces internal stress and decreases part deformation by 25% to 75%.
Lowers plastic melt viscosity, improving dimensional accuracy and product stability.
Foam injection molding can control part dimensional accuracy to 0.001 mm~0.01 mm, or even below 0.001mm. Parts produced with this technology have better mechanical properties, dimensional stability, and precision compared to traditional injection molding.
Disadvantages of Foam Injection Molding:
Radial flow marks easily form at the front of the material flow, resulting in poor surface quality and failing to meet high surface quality requirements.
Counterpressure Molding Technology
Counterpressure molding uses compressed air to pressurize the melt before it enters the mold cavity. This ensures the melt reaches the mold surface under pressure. The compressed gas prevents the growth of gas nuclei in the plastic melt by maintaining stable counterpressure, improving the dimensional stability of the parts. This process also reduces defects like depression, warping, shrinkage, and convergence lines, improving the dimensional accuracy and finish of the parts.
The startup time of the counterpressure equipment significantly affects product quality. Currently, we mainly determine the counterpressure mediator time by experience. Manufacturers widely use the combination of counterpressure and foam injection molding technology for mechanical shells, structural bases, and other high-strength applications. It is also effective for thick-walled products, reducing holding time and improving dimensional stability.
GasAssisted Molding Technology
3.1 Surface GasAssisted Molding Technology
Surface gas-assisted molding, also known as external gas-assisted molding, is used for parts with ribs, spokes, columns, bushings, or other protrusions. It compensates for volume shrinkage caused by uneven wall thickness. The gas-assisted molding principle prevents shrinkage marks on the surface while reducing internal stress. This technique also reduces deformation and warpage after injection, making it suitable for office equipment, electronic products, and high grade daily necessities.
3.2 Internal GasAssisted Molding Technology
Internal gas-assisted molding involves injecting high-pressure gases like ammonia into the mold cavity after injecting a portion of the melt. The gas creates a hollow area and accelerates the flow of the melt, filling the mold cavity. This reduces the injection pressure and the clamping force needed, and it reduces residual stress, warping, and deformation in the final product. It also improves the surface quality and produces a lighter mass with high stiffness and strength.
InMold HotCutting Technology
In-mold hot-cutting technology cuts or extrudes the cold gate before the mold opens. A high-pressure cylinder or other mechanism cuts off the cold gate during the pressure-holding period. The product separates from the gate material when the mold opens and ejects it. The cutoff surface is smooth, with no residual burrs.
In-mold hot cutting replaces traditional manual punching or milling for the gate, improving process efficiency. It solves the problem of manual pruning after the mold opens, avoiding damage to the product’s appearance and improving part consistency.
Highlight Without Fusion Mark Mold Technology
Highlight without fusion mark mold technology uses electric heating rods or high-temperature water vapor to rapidly heat the mold. During the injection process, the mold maintains pressure. After the cooling stage, the mold temperature decreases quickly, completing the injection period.
This technology improves the plastic part’s surface, making it glossy without fusion marks, flow marks, or lines. It also improves the strength and surface hardness of the part. This technology eliminates the need for polluting spray processes, reducing production costs, saving energy, and minimizing material waste.
It is especially useful for processing materials filled with glass fiber or mineral filler. This method prevents the filler from exposing on the surface, achieving a mirror effect. It widely applies in green manufacturing for home appliances, communication equipment, daily necessities, and medical devices.
Summary
The processing manufacturing industry is crucial for a strong country and the development of the national economy. Improving mold quality, adopting new processes, and using new technologies play a significant role in this advancement.