December 7, 2024
What is coordinate measurement?
The Role of Coordinate Measurement in Machinery Manufacturing
In the field of machinery manufacturing, coordinate measurement is a key technical tool, playing a critical role in product design, processing, manufacturing, and quality control. Its application significantly enhances manufacturing accuracy, product quality, and production efficiency.
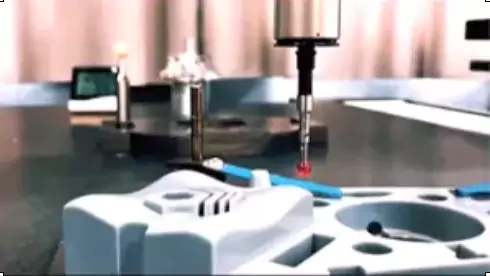
Coordinate measurement utilizes high-precision techniques to measure the spatial coordinates of an object’s surface, providing essential geometric information for manufacturing. Below, we explore the importance of coordinate measurement in mechanical manufacturing.
1.Coordinate Measurement in Product Design
Product design is the foundation of the manufacturing process. The accuracy of the design directly impacts the final product’s quality and performance. Coordinate measurement provides designers with reliable data by accurately measuring components’ size, shape, and other key parameters. This ensures that products meet predetermined requirements, reducing the need for adjustments later in the process. As a result, it improves design efficiency and guarantees manufacturability and reliability.
2.Processing and Manufacturing Accuracy
In high-precision parts processing, coordinate measurement monitors and control key dimensions during the manufacturing process, ensuring parts meet design accuracy requirements. This is particularly crucial for industries like aerospace and automotive, where product performance heavily depends on precise machining. Coordinate measurement helps protect part quality, ensuring optimal performance and reliability.
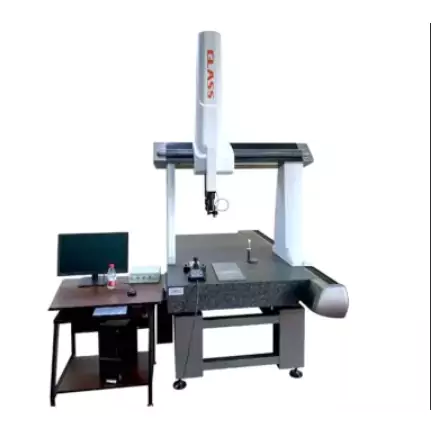
3.Quality Control in Manufacturing
Product quality is essential in machinery manufacturing, directly influencing competitiveness and consumer choice. Coordinate measurement allows for comprehensive testing of products, ensuring each component meets design specifications. By preventing defects early in the production process, coordinated measurement improves product qualification rates, reduces defects, saves costs, and enhances market competitiveness.
4.Real-Time Production Monitoring
Coordinate measurement enables manufacturers to monitor and optimize the manufacturing process through real-time acquisition and analysis of three-coordinate data. This helps in adjusting production parameters promptly, improving production efficiency, and supporting intelligent manufacturing. This approach reduces production costs, improves resource utilization, and promotes sustainable development.
Principle and Characteristics of Three-Coordinate Measurement Technology
Three-coordinate measurement technology is a vital measurement tool in mechanical manufacturing. Understanding its principles and characteristics ensures product quality and enhances production efficiency.
1. Measurement Mechanisms
Coordinate measrement technology relies on a three-dimensional coordinate system, which measures the spatial coordinates of an object’s surface. The measuring mechanism consists of three mutually perpendicular axes for X, Y, and Z movements. These axes position and locate the object to ensure accurate measurement.
The measurement probe, which can operate either through contact or non-contact, captures data from the object’s surface and calculates its 3D coordinates. The software processes and analyzes this data, generating a measurement report.
2. Characteristics of CMM
Coordinate measurement offers high precision and comprehensive measurement capabilities. The three-dimensional system provides more information than two-dimensional measurement, allowing for more accurate shape capture. The flexible measuring mechanism accommodates complex shapes and porous structures, making it ideal for high-precision measurement tasks in various industries.
However, limitations exist, such as probe contact potentially deforming soft objects and the high cost and space requirements for measuring large objects. Additionally, measurement time may be longer, making it unsuitable for high-speed production lines.
3.CMM vs Other Technologies
CMM outperforms optical measurement in handling complex surfaces and occlusions. Compared to laser scanning, CMM offers higher precision, suitable for tasks that demand stringent dimensional accuracy. It also provides more comprehensive shape and position data than two-dimensional measurement methods, ensuring greater reliability and accuracy.
Application Strategies for Three-Coordinate Measurement
1.Parts Inspection and Quality Control
Coordinating measurement technology is essential for parts inspection in machinery manufacturing, ensuring that components meet design specifications and maintaining high product quality. By using CMM, manufacturers can achieve high-precision measurement of key components, minimizing deviations and ensuring product reliability.
CMM’s ability to measure part shapes, including curved surfaces and complex geometries, sets it apart from traditional measurement methods. For example, in aerospace, CMM is used to inspect the surfaces of turbine blades, capturing detailed data to maintain quality and performance.
2.Mold Design and Manufacturing Support
Coordinate measurement plays a crucial role in mold design, ensuring the accuracy of mold parts and preventing design defects early in the process. It helps verify the fit between mold parts, ensuring that all components fit correctly for high-quality final products. During manufacturing, CMM monitors geometric features to detect errors and provide feedback, allowing manufacturers to make real-time adjustments to processes.
3.Measuring Complex Parts and Surfaces
CMM technology is indispensable when measuring complex parts and surfaces. In industries like aerospace and automotive manufacturing, where parts have intricate shapes and surfaces, CMM ensures that these components are precisely manufactured and assembled. For example, it can be used to measure the curvature of turbine blades or the surface accuracy of automotive body panels.
4.Reverse Engineering and Replica Manufacturing
Coordinate measurement technology is also essential for reverse engineering and replica manufacturing. It enables the creation of digital models from existing parts by capturing their geometric parameters. In applications such as aircraft engine blade replication, CMM ensures that the replica maintains the same quality and performance as the original. Reverse engineering offers time and cost savings by allowing faster access to product data and reducing the need for extensive prototyping.
Conclusion
Coordinate measurement technology is a cornerstone of modern mechanical manufacturing. Its ability to ensure high-precision measurements across product design, manufacturing, quality control, and reverse engineering makes it an invaluable tool. Understanding its principles, advantages, and limitations helps manufacturers optimize their processes, improve product quality, and remain competitive in an increasingly demanding market. As technology advances, the role of coordinate measurement will only continue to expand, driving the future of manufacturing.